Project Description
IHT Automation
Automatic Process Control, Cutting Torches and Height Control Systems for Oxy-Fuel and Plasma Cutting Machines
OXY-FUEL
Autogen (Oxy-Fuel) cutting belongs to most popular steel cutting technologies. As it is mechanized technology, it is often used on 2D gantry cutting machines (tables) but also as 3D with robots and various types of rotators. Autogen is relatively complex technology where high level of process automation is required to achieve maximal performance and cut quality.
Gas parameters adjustment, flame ignition, flame setting, clearance control, slag, backfire, collision detection, … material preheating, piercing, cutting speed … these are the words with many others which are used by experts when cutting process is set up. IHT Automation provides „click and cut“ automated systems. All these complex words can be forgotten by user because they, and all what is behind them, are embedded in the system. The combination of the best single components has been selected to build up the systems. Not only long-term experience of generations of experts but also the actual information collected from the customers stays behind the systems parameters.
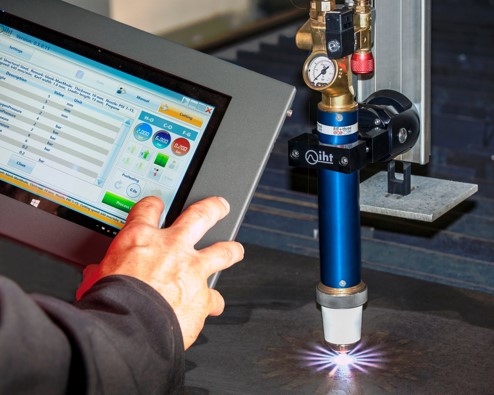
Oxy-Fuel Solutions and Systems
The word „Solution“ in meaning of Oxford Dictionary: “Products or services designed to meet a particular need”, „Solving a problem or dealing with a difficult situation“.
APC is the solution, the complete Oxy-Fuel cutting process in one system. It is the latest development of IHT Automation. It guides users across all the difficult routes on the way to perfect cut. It guides also Machine builders during their integration and commissioning.
Multifunctional and robust, this are the characteristics of all IHT cutting systems. Cutting is based on FIT+ high-speed technology with intelligence included in FIT+ three cutting torch. Most traditional IHT product best in class capacitive height sensing, flame ignition and many other features are newly integrated in the system. IHT M 4000 torch lifter is famous in the industry by its reliability and long-live.
Products
Automated Process Control Oxy-Fuel Cutting systems
APC is an Oxy-Fuel cutting system with Cutting Torch, Gas Control, Flame Ignition, Height Sensing and Lifter, all in one package. The cutting database for FIT+ three torches is either stored in the Operator Terminal or directly implemented in the machine control (CNC).
Process: Oxy-fuel
Features
- Cutting process is integrated into APC system
- Cutting Database, integrated automated Ignition, Preheating, Piercing and Cutting operation
- Fits on all carriages
- Only requires oxygen and fuel gas connection
- Gas distribution, safety and electrical components are part of the package
- Gas Controller mounted close to the torch, one controller per torch
- Works with all common CNC controllers on the market
- Modular approach allows highest flexibility
- Setting torch height in mm or inch
- Short torch to torch distance
- Cutting close to edge and kerf
- Best in class height sensor for dry cuts
- Flash back detection to extend torch lifetime
- Slag detection
- In cutting torch integrated ignition
- Tool free nozzle exchange, high speed, high quality cutting
Application Fields
- Oxy-Fuel cutting machines for straight cutting of up to 300 mm sheets
- Single or multi torch applications, one Gas Controller per torch
- 100 % compatible with the plasma systems IHT M 4000 PCS and M 4000 BAS
- Solution for new cutting machines and retrofits
- Cut sheets up to 100 mm thickness when used with active height sensor and up to 300 mm with Splash Protector
Automatic Process Control for Oxy-Fuel Cutting with a Robot
APC for Robot is an Oxy-Fuel cutting system with Cutting Torch, Gas Control, Flame Ignition and Height Sensing, all in one package. Height control has to be performed by the robot. The cutting database for FIT+ three torches is either stored in the Operator Terminal or directly implemented in the machine control (CNC).
Process: Oxy-fuel
Features
- All in one package: Oxy-Fuel Cutting System with Cutting Torch, Gas
Control, and Flame Ignition Cutting Database, integrated automated Ignition, Preheating
Piercing and Cutting operation - Fits on all robot arms
- Only requires oxygen and fuel gas connection
- Gas distribution, safety and electrical components are part of the
package - One Gas Controller per torch
- Gas Controller to be mounted close to the torch
- Works with all common CNC controllers on the market
- Modular approach allows highest flexibility
- Flash back detection to extend torch lifetime
Application Fields
- Oxy-Fuel cutting robots for cutting of up to 300 mm sheets
- Straight cutting, bevelling, 3D cutting, scrapping
- Single or multi torch applications
- Solution for new robots and retrofits
- Plate piercing up to 100 mm thickness with active Height Sensor and
up to 150 mm with Splash Protector (vertically, downwards oriented
torch) - Cutting from the edge with active Height Sensor up to 300 mm
plate thickness (vertically, downwards oriented torch)
Oxy-Fuel Torches
Products
Oxy-Fuel Machine Cutting Torch with Height Sensing* and Integrated Ignition
- Increased cutting machine performance thanks to unique IHT height sensing system
- Integrated torch electronics can easily be connected to CNC systems
- Torch Controller with two modes: Remote setpoint (position) or height measurement output
- Tool-free nozzle and sensor system means reduced downtime
- Integrated control valves for heating oxygen and fuel gas for a quicker installation
- Built in pressure gauge for cutting oxygen improves cut quality
- Flashback detection for safe operation and longer life time
Application Fields
- Oxy-Fuel cutting machines with integrated z-axis and motor controller
- The Torch Controller, attached to the Sensor Torch handles all required signals shown under CNC connections
- Cutting sheets to 100 mm thickness used with active height sensor and up to 300 mm with Splash Protector
- Height sensing for dry cuts
Deviation Mode
- In: Setpoint (0-10 V)
- In: Ignite
- Out: Deviation Position (0-10 V)
- Out: in Position
- Out: Error/Collision/Flashback
- Power: 24 V DC / 0,6 A
Height Mode
- In: Calibrate Height
- In: Ignite
- Out: Torch Height (0-10 V)
- Out: Error/Collision/Flashback
- Power: 24 V DC / 0,6 A
Oxy-Fuel Machine Cutting Torch with Integrated Ignition
- Automatic ignition system build into the torch
- Improved productivity of the Oxy-Fuel cutting machine due to use of high-speed cutting nozzles
- Fast installation and safe operation with integrated control valves
- Easier for machine operators to handle thanks to use of Tool-Free Nozzle changing system
- High speed cutting nozzles for further improved cutting quality
Application Fields
- Oxy-Fuel cutting of straight and shaped cuts in accordance with ISO 9013
- Oxygen cutting from 3 to 300 mm
- Hole piercing up to 150 mm
- Can be used with different fuel gases
- Compatible with all cutting machines
- Suitable for new installations as well as retrofitting
- Special solutions for water tables or Hardox cutting (please contact us if required)
Connections
- In: Ignite 24 V DC / 1 mA, start ignition command
- Out: Error
- Power 24 V DC / 1 A
- Earth / Ground
In:= from CNC
Out:= to CNC
Oxy-Fuel Machine Cutting Torch
- Unique system for Oxy-Fuel machine cutting technology
- The product concept created based on the long-term partnership with the customers
- High productivity of Oxy-Fuel machine cutting process due to high-speed cutting nozzles
- Safe operations and high resistance against flashback ensured by integrated COOLEX® and axial injector with application of Resonator Mixing system in acetylene variants
- Working efficiency with minimized nozzle exchange time
- Easy to handle for machine operators because of Tool-Free nozzle changing system
- Nozzle fixation done manually by special bayonet system, without any wrench
- One type of heating nozzle for all fuel gases
- Extended lifetime of consumable nozzles
- Conform to ISO 5172
Application Fields
- Oxy-Fuel cutting of straight and shaped cuts in accordance with ISO 9013
- Oxy-Fuel cutting from 3 to 300 mm
- Hole piercing up to 150 mm
- Can be used with different fuel gases
- Compatible with all cutting machines
- Suitable for new installations as well as retrofitting
The integrated clearance sensor system ISC is a logical next step of IHT sensors for oxy fuel dry cutting. It combines the excellent quality of the machine cutting torch and the unreached IHT sensor system for oxy fuel cutting. It allows oxy fuel cutting with higher quality and improved productivity.
The integrated sensor system is available with cutting torches from Messer (ISC 1), Harris (ISC 5) and GCE (ISC 8).
The sensor system ISC 8 is using the machine cutting torch FIT+ from GCE. The torch will be supplied by IHT and is an integral part of the sensor system. For cutting nozzles please check list under “Accessories“.
To complete your ISC height control system, please add a M 4000 ISC or CSC 500 ISC system.
Advantages
- No Ring Electrode and additional cabling
- Detect slag, no collision
- Better work piece utilization through cutting close to edge and kerfs
- Due to the shape of the sensor, the system can be used for height control during bevel cutting
- Quick disconnect facility to allow quick changing of nozzle
- Works together with well established M 4000 ISC or CSC 500 ISC systems
Harris Oxy-Fuel Machine Cutting Torch with IHT Height Sensing
The integrated clearance sensor system ISC is a logical next step of IHT sensors for oxy fuel dry cutting. It combines the excellent quality of the machine cutting torch and the unreached IHT sensor system for oxy fuel cutting. It allows oxy fuel cutting with higher quality and improved productivity.
The integrated sensor system is available with cutting torches from Messer (ISC 1), Harris (ISC 5) and GCE (ISC 8).
The sensor system ISC 5 is using the machine cutting torch 198-2T and -2TF from Harris. The torch will be supplied by IHT and is an integral part of the sensor system. For cutting nozzles please check list under “Accessories“.
To complete your ISC height control system, please add a M 4000 ISC or CSC 500 ISC system.
Advantages
- No Ring Electrode and additional cabling
- Detect slag, no collision
- Better work piece utilization through cutting close to edge and kerfs
- Due to the shape of the sensor, the system can be used for height control during bevel cutting
- Quick disconnect facility to allow quick changing of nozzle
- Works together with well established M 4000 ISC or CSC 500 ISC systems
Messer Oxy-Fuel Machine Cutting Torch with IHT Height Sensing
The integrated clearance sensor system ISC is a logical next step of IHT sensors for oxy fuel dry cutting. It combines the excellent quality of the machine cutting torch and the unreached IHT sensor system for oxy fuel cutting. It allows oxy fuel cutting with higher quality and improved productivity.
The integrated sensor system is available with cutting torches from Messer (ISC 1), Harris (ISC 5) and GCE (ISC 8).
The sensor system ISC 1 is using the machine cutting torch MS 932 or optionally MS 832 Torch. The torch will be supplied by IHT and is an integral part of the sensor system. For cutting nozzles please check list under “Accessories“.
To complete your ISC height control system, please add a M 4000 ISC or CSC 500 ISC system.
Advantages
- No Ring Electrode and additional cabling
- Detect slag, no collision
- Better work piece utilization through cutting close to edge and kerfs
- Due to the shape of the sensor, the system can be used for height control during bevel cutting
- Quick disconnect facility to allow quick changing of nozzle
- Works together with well established M 4000 ISC or CSC 500 ISC systems
External Igntion System
This Oxy-Fuel ignition system is designed to be used with cutting machines fitted with either propane or acetylene torches. It is fully compatible with the following IHT Oxy-Fuel height control systems; CSC 500, M 4000 CAP, M 4000 ISC and M 4000 TWIN.
Process: Oxy-Fuel
The ignition system is characterized by
High productivity
as a result of the incorporated automatic ignition system
- When used in multi-burner systems, process times can be reduced
- Reduced gas consumption
- Available for both propane and acetylene torches
Increased reliability
- Possibility to increase the distance between the torch tip and workpiece
- Ignition burners protected from slag
- No high voltage ignition required
- Gas supply mechanically protected
Simple installation and commissioning
thanks to the fully integrated design
- System components are selected for full compatibility
- Simple connection to CNC control system
- No oxygen supply necessary
- 24V signal for ignition
PLASMA
IHT’s Plasma height control systems are compatible with both gantry machines as well as flatbed machines. Please note that the distinction between simple standard applications (e.g. air plasma) and high quality applications (using high quality plasma) should be made.
All Plasma systems can operate stand alone or operated from the CNC using our “CUTBUS” interface.
There are modular systems based on our well proven M 4000 architecture or compact systems called B 1000.
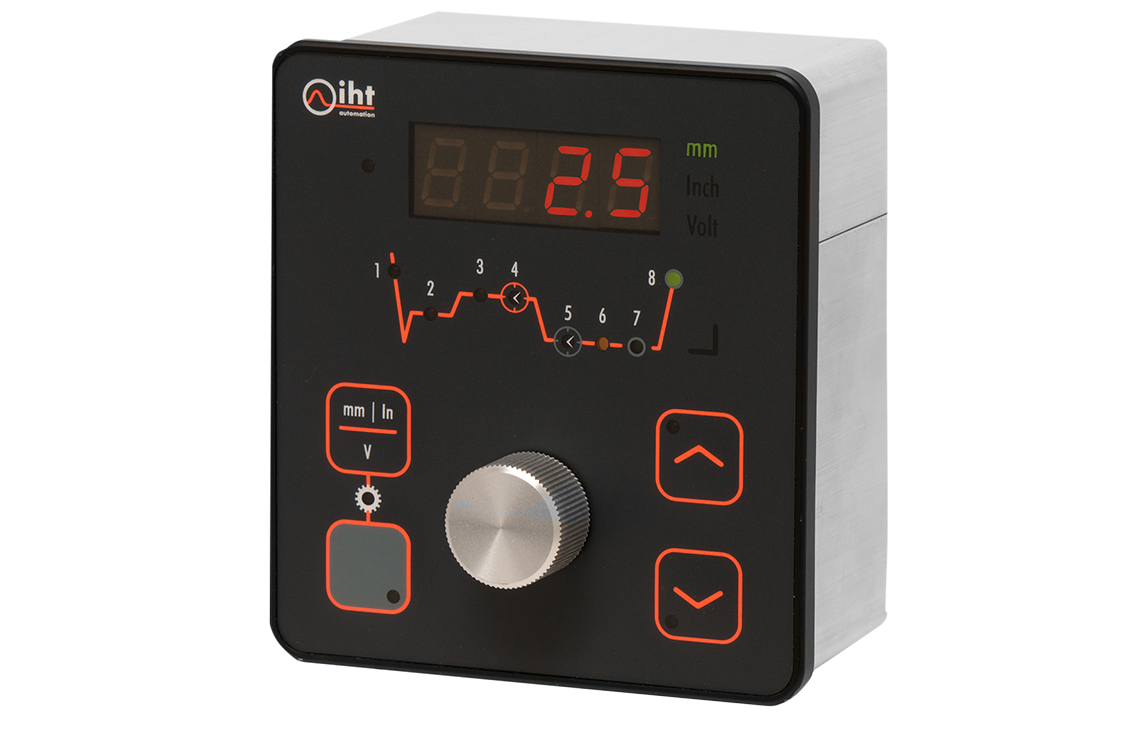
Plasma Height Control Systems
Products
Automatic clearance control for plasma cutting machines
The M 4000 PCS can be operated from its own operator terminal or centrally controlled by a CNC machine. It is suitable for cutting any kind of plasma compatible material, for underwater cutting or for cutting thin metal sheets. As standard the initial position finding is tactile but the optional IHT nozzle sensor can be used if non-contact position finding is required (Dry plasma only).With the clearance being adjusted in 0.1 millimetre steps, a constantly high cutting quality and performance is obtained, the distance between plasma nozzle and workpiece being measured and controlled by the arc voltage.
Another option is the CUTBUS® signal for automatic transfer of cutting parameters from the CNC system to the LINEAR DRIVE. The torch is protected by built-in 3D collision detection in the torch clamp and there is vertical and horizontal collision detection to avoid other damage.
All torch lifter parameters can be set up and changed during operation using the multi-language operator terminal.
Process: High Quality Plasma
Advantages
- Clearance can be set in inches, millimeter or arc voltage
- Accurate clearance control during plasma cutting
- High yield from the work piece due to capability to cut closer to edges and corners
- Increased elevation height during piercing increases component lifetime
- Enhanced cutting quality with automatic detection of cuts and corners
- Adjustable gas pre-flow for increased cutting speed
- New 3D-collision protection with intelligent collision avoidance
- CUTBUS® Network enabled.
Automatic clearance control for standard plasma cutting machines
One of the most important components when cutting with plasma is the precise clearance control.
The M 4000 BAS system provides all required characteristics for a precise cut. The system adapts to all common cutting machines, regardless if new installations or retrofit.
Process: Plasma
M 4000 BAS consists of the LINEAR DRIVE BODY BAS, the GUIDING RAIL with 220 or 350 mm stroke and the OPERATOR INTERFACE with a built-in arc control system, motor controller and operator panel.
The operation of the M 4000 BAS system is done by BAS OPERATOR INTERFACE and digital signals and can be operated manually or centrally via a CNC. The setting of pierce height and cutting height is in millimeter, the setting of pierce delay in seconds. The control of cutting height is done using the ARC voltage.
The torch is protected using excellent 3D collision protection in the torch clamp and a vertical collision detection.
Options: Collision detection and Contact Sensor
Electronic components are identical to B 1000, details see B 1000 Brochure.
OFFICE LINE
1.800.555.6789
EMERGENCY
1.800.555.0000
WORKING HOURS